Installing a spray paint booth for your operation is no small task. They are a critical aspect of safely applying coatings in your facility and installing your spray paint booth requires numerous parts and a lot of manpower. An essential facet of this installation process is making sure your booth achieves code compliance. Almost every business is subject to safety and environmental regulations and codes on both a local and national level. Since spray booth operations generally present a higher risk of fire and hazardous exposure, owners are responsible for meeting several sets of minimum standards enforced by different agencies. When facing differences between local and federal rules, companies are often required to meet the one with the stricter requirements. Your insurance company will in all likelihood require stricter fire suppression requirements to:
- Help mitigate against losses
- Reduce property damage exposed to potential fire damage
- Reduce exposure to business income loss were a fire or explosion to occur
- Minimize the chances of damage to high value vehicles were an explosion to occur
- Reduce the chances of damage to neighbor’s property due to an explosion or rapidly spreading fire
- Reduce the chances of bodily injury to employees or the public
In a perfect world, achieving code compliance would be a one-size-fits-all activity. In reality, however, many standards apply and different localities have varying ordinances and permit requirements. This results in many variations dependent on your location.
Before the first vehicle can be moved into your spray booth it is important to understand what standards and regulations apply to your facility and what you must do to ensure the safety of your workers and protection of your equipment and property. By understanding the related rules and codes of your paint booth you can better understand why they are required for spray operations as well as safety factors that you should consider with the use of your paint booth. By understanding the codes that are applicable to your operation, your booth can be built and assembled in accordance with multiple national and international standards.
There may be situations where you already have a spray paint booth, purchased one listed as meeting Underwriters Laboratories (UL) standards, or even purchased an existing booth from someone else that is disassembled and re-assembled which does not have a fire suppression system. Operating a spray paint booth without a fire suppression system is a risk that threatens the safety of those using the booth, any parts or vehicles being painted as well as your entire facility. It is in your best interest to work with someone knowledgeable in code compliance to identify which codes are applicable so that you can bring your spray paint booth into compliance and in turn minimize those associated fire risks.
There are many things you can try to do-it-yourself, spray paint booths are not one of them. You should consult with professionals that have the know-how and experience to make sure your booth will be up to code not only as it is built but also as codes and regulations change. For many operators, a professionally-engineered booth is the most effective and economical way to apply spray and finish compounds responsibly. While booths mitigate many of the risks associated with the application of volatile or hazardous substances, they can only do this if operators maintain their system and keep it in full compliance with applicable regulations.
There are several codes and regulatory standards that are used by various local governments and even your insurance company for defining spray booth requirements. Each state, county and city usually selects one of these codes as the main top-level code to reference requirements. Some local governments will create their own codes based on special requirements, but they often use one of the main standards as a guide. You obviously must first work with your local fire officials and meet the requirements that they have set for spray booth operations. This is an essential aspect of getting started.
The four most common regulatory bodies related to paint booths in the United States include the National Fire Prevention Association (NFPA), Occupational Safety and Health Administration (OSHA), International Fire Code (IFC) and Environmental Protection Agency (EPA). Each agency has varying roles in relation to spray applications and safety. In this paper we will cover some of the primary areas that each organization works relating to paint booths. This is by no means an exhaustive list but merely intended to provide an overview of what is involved. If you have questions it is ideal to speak with the organizations directly and coordinate with the appropriate local authority from each agency to ensure you have a full understanding of all safety regulations in relation to paint booths.
NFPA
The National Fire Protection Association (NFPA) is the leading global advocate for the elimination of death, injury, property, and economic loss due to fire, electrical and related hazards. They deliver information and knowledge through more than 300 consensus codes and standards, research, training, education, outreach and advocacy. Since fire is always a risk when running a spray booth, operators are subject to many of the regulations set forth by the NFPA, especially NFPA-33 National Fire Protection Association's Standard for Spray Application Using Flammable or Combustible Materials. This is the most common code and does a very good job of defining how a spray booth is designed and constructed, air flow requirements and fire protection. This standard references many other lower level standards such as NEC (National Electric Code), NFPA-101 Life Safety code and NFPA-17 Dry Chemical Extinguishing Systems.
A few small scale spray paint operations may not meet NFPA 33 requirements. You can use the following flow chart to evaluate your own operation:
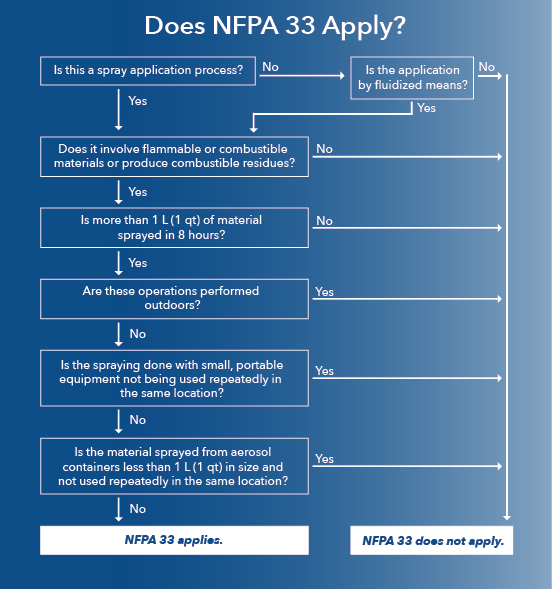
OSHA
The Occupational Safety and Health Administration (OSHA) is the primary United States federal agency responsible for regulating safe spraying operations in the workplace, including air quality, fire control systems, protective equipment, lighting, acceptable levels of substance exposure and the separation of hazardous operations from the rest of the workplace. Each state has regulations and standards that cover worker safety. Many states adopt the federal requirements.
OSHA's 29 CFR1910 Occupational Health and Safety Requirements – ensure employee safety, minimize health risks and reduce liabilities for facility owners. These regulations are updated on a regular basis, so the best way to ensure full compliance of your spray booth operations is to stay informed.
Every spray booth constructed in the U.S. that is used in a workplace environment is required to comply with OSHA regulations and standards, so it is important for spray booth owners and operators to understand that regulations are enforceable long after the booth is completed. A spray booth will be certified to the current NFPA or IFC code only when it is being constructed, but it must always comply with OSHA requirements.
Generally speaking however, OSHA's primary role in relation to paint booths is overall safety. Particular areas that OSHA is concerned with include painter safety and safety of the spray environment. They offer an overview of pertinent safety information here. Important areas of consideration include adequate space around the paint booth, electrical safety near painting operations, fire extinguishing regulations for paint booths, and operator safety including storage of chemicals as well as safety equipment. OSHA has a listing of local offices here. Coordinating with your local office will help to ensure you have a full understanding of all the aspects of safety that OSHA oversees.
In addition, OSHA has requirements for the design of equipment and operations involved in spraying flammable or combustible materials. In most cases however, compliance with NFPA 33 is acceptable to meet OSHA's requirements.
IFC
Much like the NFPA standards, the International Fire Code (IFC) is an established code that addresses fire risks in the workplace. While these regulations are not used universally in the United States, dozens of state governments have adopted it for use in their jurisdiction. This international standard is a short and slightly modified version of NFPA-33. It does not have more or less stringent requirements than NFPA-33 but some requirements are included in sections outside of the spray booth chapter. This code is commonly used in areas of international trade zones. Additionally, some state government agencies require full compliance of the International Fire Code, a code that enforces regulations on fire safety and prevention in the workplace. Depending on your location, certain local building codes, fire protection agencies and environmental agencies might enforce additional requirements that operators need to comply to.
EPA
The Environmental Protection Agency (EPA)relates to paint booths as they are often concerned with the volume of volatile organic compounds (VOC's) you produce. VOC's are compounds that are harmful to the atmosphere that are present to varying degrees in coatings. The EPA has offices in each of the states and in addition to national regulations, states often have regulations related to VOC's as well.
Conclusion
Ultimately, establishing a spray paint booth has a lot that you need consider. Worker safety must be taken into consideration as well as the safe operation of your booth. The many codes and regulations regulating your operation are in place to make your spray paint booth a safer one – safer for you, safer for your employees and safer for your business. This is not an easy task. Evaluating a paint booth requires complex engineering calculations and numerous regulations and codes. Your operation would be best served by using a knowledgeable and experienced firm with the knowledge to assure your operations are working efficiently and within code compliance.
References
- http://www.spraysystems.com/news/what-does-my-booth-need-to-be-code-compliant
- https://globalfinishing.com/2011/06/22/paint-booth-code-compliance-what-you-need-to-know-and-why/
- http://www.spraysystems.com/booth-codes
- https://www.hppneumatics.com/minimum-requirements-paint-booth/
- https://pittsburghsprayequip.com/blogs/pittsburgh-spray-equipment-company/paint-booth-code-compliance-safety-regulations
- https://globalfinishing.com/2018/09/20/what-does-my-paint-booth-need-to-achieve-code-compliance
- https://www.toolsusa.com/blog/spray-paint-booth-codes-and-regulations/
- NFPA
- OSHA
- IFC
- EPA